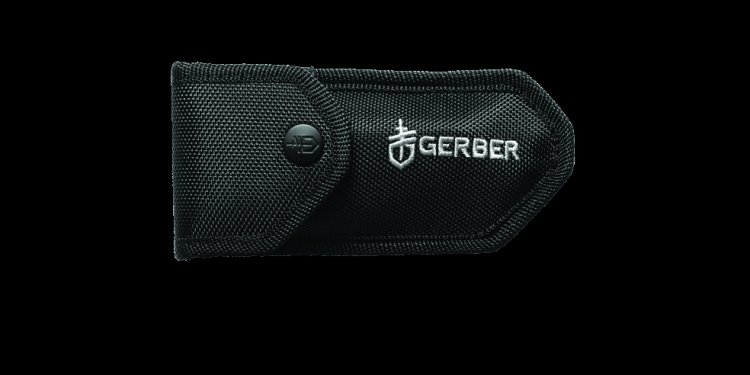
Gerber Knife Holsters
We’ve all been there… you like the knife but hate the sheath. Or, you lost a sheath. Or, you’ve made your own knife that now needs a sheath. If you are an outdoors man, at some point in your life you are going to have a knife but no sheath. Without a sheath you can’t really carry the knife which means that you can really use it in the field. It might as well stay in your kitchen to cut up tomatoes. What a waste.
If your knife is “sheathless” you pretty much have 4 choices:
- Find a sheath from another knife that fits well enough to make due (this never turns out well)
- Make a leather sheath yourself (easier said than done – this is a true skill and requires several leather working tools)
- Hire someone to make a custom knife sheath (Get ready to pay out some big bucks)
- Make your own custom kydex sheath. (Affordable and fairly simple with no expensive tools)
Some of the most expensive knives on the market come with Kydex sheaths – Tom Brown Tracker & Becker BK2 for example.
Kydex is an extremely durable and functional sheath material. It also just happens to be very inexpensive and easy to work and mold with simple tools you probably already have at home. This was the first Kydex sheath I ever made and it took me only about 1 hour.
Kydex is a thermoplastic material that can be heated up and molded while hot and soft. Once cooled it retains it’s rigid and almost indestructible texture and properties. It is extremely popular for knife sheaths and gun holsters. It is water resistant and is pretty much hassle free. Bottom line – it’s functional.
Interested in your own Kydex Sheath Build? Read on….
I recently bought a Gerber BIG ROCK camp knife. It’s a really great fixed blade knife. I wanted a descent knife to keep in my Bronco and this one fit the bill – and it was only $39. The only problem – I just didn’t like the sheath. So, I decided to make a custom sheath using Kydex I ordered from .
To make a kydex sheath you really only need 7 ingredients:
- A section of Kydex sheeting
- Some rivets and rivet punch
- A Belt fastener (for carrying your knife on a belt)
- An oven or toaster oven
- A drill with some bits
- Hobby saw or Band Saw
- A foam press for pressure molding the heated/soft kydex around your knife (homemade)
By the way – I’ve seen many people making custom kydex sheaths and holsters for knives, guns, flashlights, etc… on the side for part-time income. It can be a great hobby for gifts or a side business. Everyone has their own skill-sets. You never know, you may become a Kydex Craftsman.
I ordered everything ala-cart from but if I had it to do over again I would have ordered this kit for $10.95: KYDEX KNIFE KIT
It includes the following:
- (1) 12×12 piece of .060 KYDEX material (cell/smooth finish).
- (1) Ball chain 20 lb pull (breaking strength) This chain is common on neck style knives.
- (10) #8 – 8 black rivets. Requires a .25 inch hole in the sheath for fastening.
- (1) 2″ Belt Size Capable, Matching Color Custom Pre-formed CKK Design Kydex Belt Loop (w/fastening hardware)(Vertical/Horizontal carry) Universal Mounting Design
Once you have everything rounded up and about an hour to invest, it’s time to determine your sheath size. This doesn’t have to be exact because you can trim it down later. Error on the side of too big. Make sure the piece you cut is wide enough to cover your blade when folded over – I made mine wider to include space for a fire steel. Also make sure it is long enough to cover the blade and about 1 inch up the handle.
Mark the kydex with a pencil and score it with a knife or razor. Then you can break it fairly easily.
I had plenty left over for another project later…
In order to form the heated kydex sheet around your blade (or other object) you need to press the heated and pliable kydex sheet in a foam press. You can buy these but they are pricey. If you really get into making these it would be a good investment. I made one out of an old foam thermarest seat and used a vice to apply the necessary pressure.
As you can see I cut 2 equal sections out of the seat and simply glued them to 2 scrap pieces of 1/2″ press board. Your foam needs to be at least 1.5″ thick. Have your vice nearby and ready to go.
I tossed my cut kydex sheet onto a baking pan and put it in the oven at 300 degrees and checked it every few minutes. It took about 10 minutes to get nice and soft and pliable. USE GLOVES. Once it was pliable, I took it out and folded it over my knife blade…
I folded mine from side to side but I suppose you could do it from end to end as well. I wanted to create a pocket on one side, though, for a fire steel. DON’T WORRY – if you screw this up all you have to do is toss the kydex back in the oven and it goes back to it’s original shape. I had to do this part 4 or 5 times to get it right. You also have to work fairly quickly because as the kydex cools it hardens. This all has to be done while it is nice and pliable in order to work properly.
Quickly, I sandwiched the knife and kydex wrap between my foam lined board and winched it down in the vice as tight as I could get it. WAIT 10 minutes. (This, too, I did several times.)
It took me a few tries but eventually I ended up with this rough shape out of the press. I decided to incorporate a fire steel which was a little tricky. It would have gone quicker if I just stuck with the basic sheath. Notice the kydex comes up over the handle about 1/2 to 1″. This is important because it’s this section that holds your knife in the sheath once you are finished.
Once you take the knife out of the press, it’s time to draw on your final sheath design.
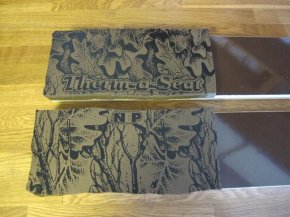
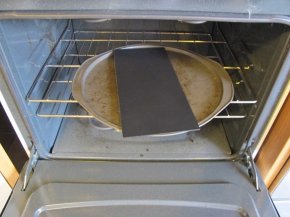
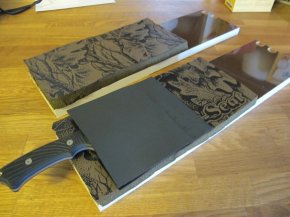
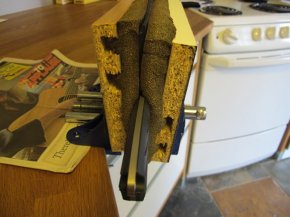